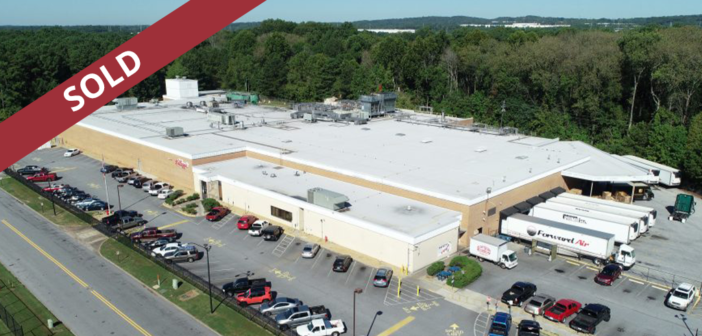
100,000 SqFt Frozen Bakery Plant
5601 Bucknell Dr SW, Atlanta, GA
Property Description
Atlanta, GA – Available Turnkey: 100,000 SqFt Frozen Bakery and Breakfast Product Plant
Ample Parking, Warehouse Attached to Production, Fenced Property with Guard Shack, Complete with (4) Stand Alone Spiral Freezers, Ambient Spirals, (5) Flow Wrapping Packaging Lines with Feed Conveyor, Late Model High-End High-Speed Cartoners and Case Packing, Processors, Pumps, Batter System, X-Ray, Metal Detection and Checkweighers, Engine Room, Plant Air System and All Support.
Brochure
Download BrochureBuilding Summary
USE & OCCUPANCY
- Designed for high-volume frozen waffle production
- Currently configured for two (2) dual lines, in-feeding four (4) spirals
- Refrigerated vestibule with six (6) fully-equipped dock doors
- Rigorous third-party food safety and employee safety compliance (GMP, HACCP, SQF, AIB)
- Highly efficient workforce (150 total / 40 1st shift)
- Prestigious location in 4,600-acre, 46.1M square foot, 553-building Fulton Industrial District
PRODUCTION INFRASTRUCTURE
- 10,000 lb. ammonia system with four (4) JBT / Northfield spirals and finished goods freezing
- Two (2) 100,000 lb. flour silos, with gravity flow mixing, sifting, mixing and batching
- Two (2) bulk liquid oil storage tanks, with a working volume of 9,000 gallons each
- Three (3) 200 hp Ingersoll Rand air compressors, with extensive intra- plant distribution
- Two (2) gas-fired hot water systems: Process @ 300 gpm, and domestic at 38 gpm
- Waste pre-treatment (anaerobic bio-digester)
- QA Lab
STRUCTURE & UTILITIES
- Original construction in 1969
- 100% roof installed in 2011
- Brick exterior walls, concrete block interior walls, and sealed, sloped, and drained concrete floors
- Dropped ceilings from 14’ to 17’ clear, with approximately 3 additional feet to the joist, to 20′ clear
- Wet sprinkler
- Linear configuration and flow
- Full perimeter fencing, with three (3) gated access points, one with guard station with monitored surveillance
- Twin-bay interior loading, with five (5) fully-equipped outgoing truck docks
- Georgia Power: Two 2,500 kva transformers, with 477 / 280 volt, three-phase, 4-wire secondary
- Georgia Natural Gas: 1.25” high pressure line to site, regulated to 5 psi with 3” internal piping
- Department of Watershed Management: 8” process and 100 psi 8” fire line
DUE DILIGENCE
- Zoned M-1A Industrial Park
- Property Taxes: 2017 taxes (unchanged from 2016) were $38,471 ($0.39 SF) for the plant and 6.89 improved tract
Equipment Summary
- Extensive front-end ingredient sifting, mixing and batching
- Five (5) flow-wrapping lines feeding two (2) newer carton and case packing lines with X-ray inspection
- Complete bulk ingredient, refrigeration, compressed air, sanitation, and waste pre-treatment systems and infrastructure
Share